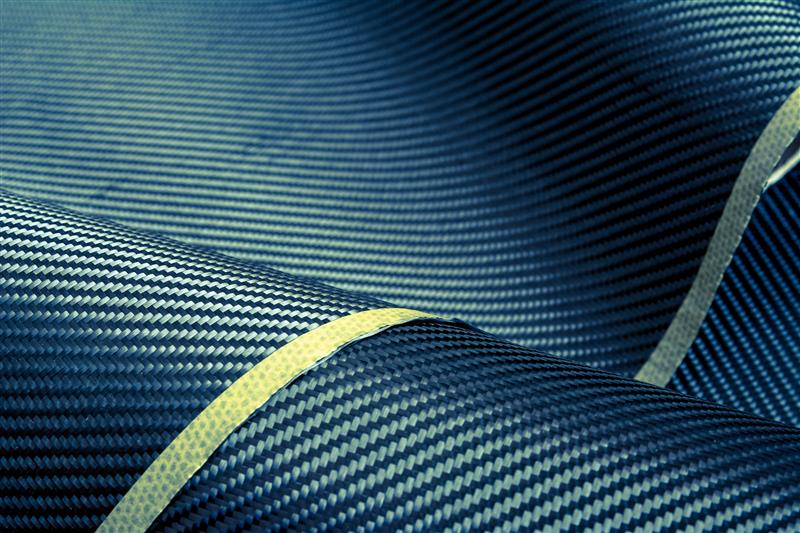
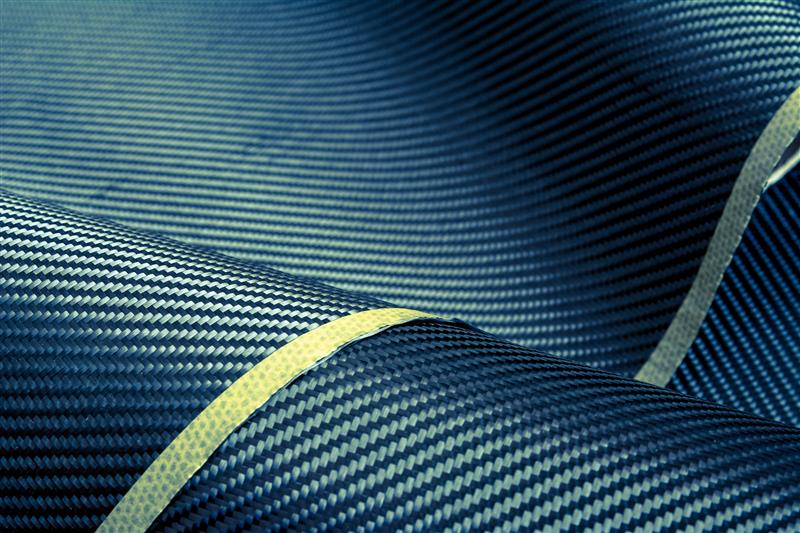
Prepregs In Advanced Manufacturing
Makobond Prepregs are precision-engineered composite materials consisting of reinforcement fibers or woven fabrics pre-impregnated with a precisely formulated, pre-catalyzed resin system. These advanced materials offer controlled resin content and distribution, ensuring exceptional consistency and superior mechanical properties compared to traditional wet lay-up processes. With extended room-temperature working times and cure activation only upon heating, our prepregs allow greater production flexibility. Makobond prepregs also support your sustainability goals, reducing material waste and emissions through controlled resin usage and enabling cleaner manufacturing practices.
KEY FEATURES
Optimal Resin
Ratios
Consistent and precise resin-to-fiber distribution ensures reliable mechanical properties and high-performance results.
Extended Shelf
Stability
Long shelf life with variable temperature storage options supports flexible handling and inventory management.
Precision Curing
Processes
Cures through controlled heating methods, enabling precision and repeatability in manufacturing.
High Strength for
Complex Geometries
Engineered for lightweight structural applications, even in intricate or contoured part designs.
Sustainable
Composite Solutions
Minimizes waste and VOC emissions with environmentally conscious material formulations.
Speak with our Technical Sales Team
Prepreg
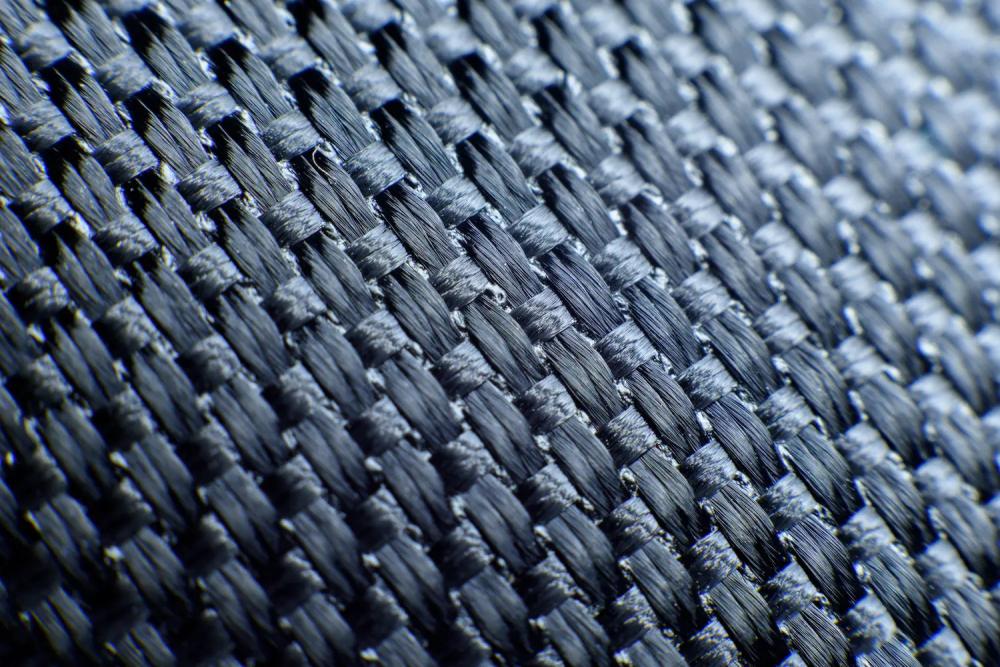
Epoxy Prepregs
Epoxy prepregs are among the most versatile composite materials used in manufacturing today. Known for their exceptional mechanical strength, durability, and environmental resistance, epoxy prepregs are ideal for aerospace structures, automotive components, and industrial tooling. Makobond epoxy prepregs are designed for easy processing and consistent resin content, making them a reliable solution for high-performance parts. Whether reinforced with carbon fiber, fiberglass, or aramid fibers, epoxy prepregs deliver reliable performance in structural and non-structural applications.
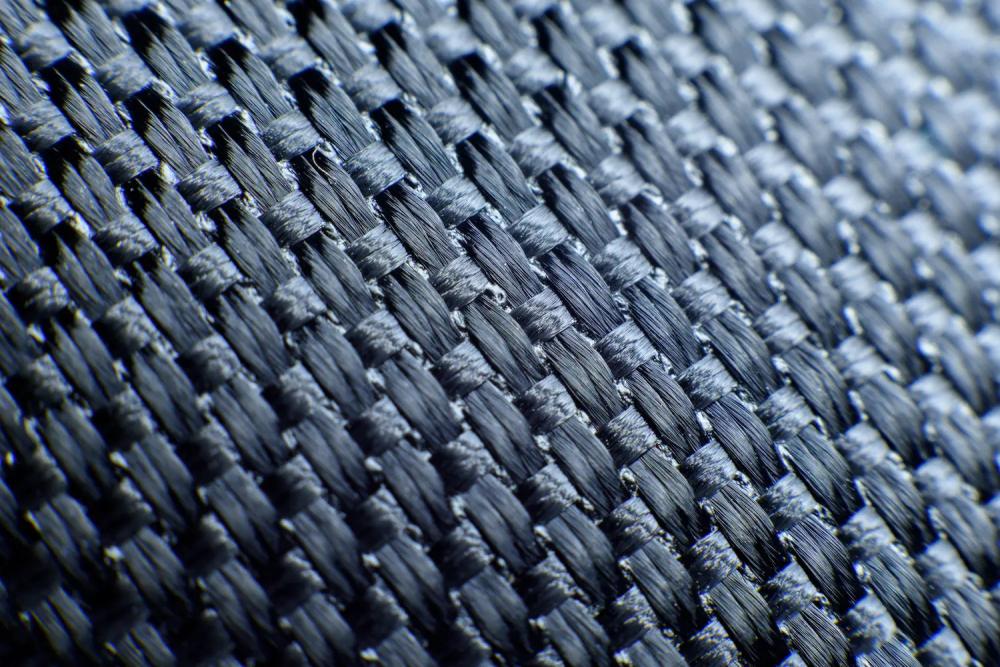
BMI Prepregs
BMI (Bismaleimide) prepregs are high-temperature composite materials designed for aerospace and defense applications. Known for their thermal stability up to 450°F (232°C), Makobond BMI prepregs are ideal for APU ducts (Auxiliary Power Units), leading edges, engine surrounds, high-performance military aircraft, and payload fairings, where thermal loadings are a dominant design condition. Makobond BMI prepregs offer excellent hot/wet performance, dimensional stability, and flame resistance, making them a trusted solution for environments where heat and safety requirements are critical. These prepregs meet demanding aerospace specifications for long-term durability in extreme conditions.
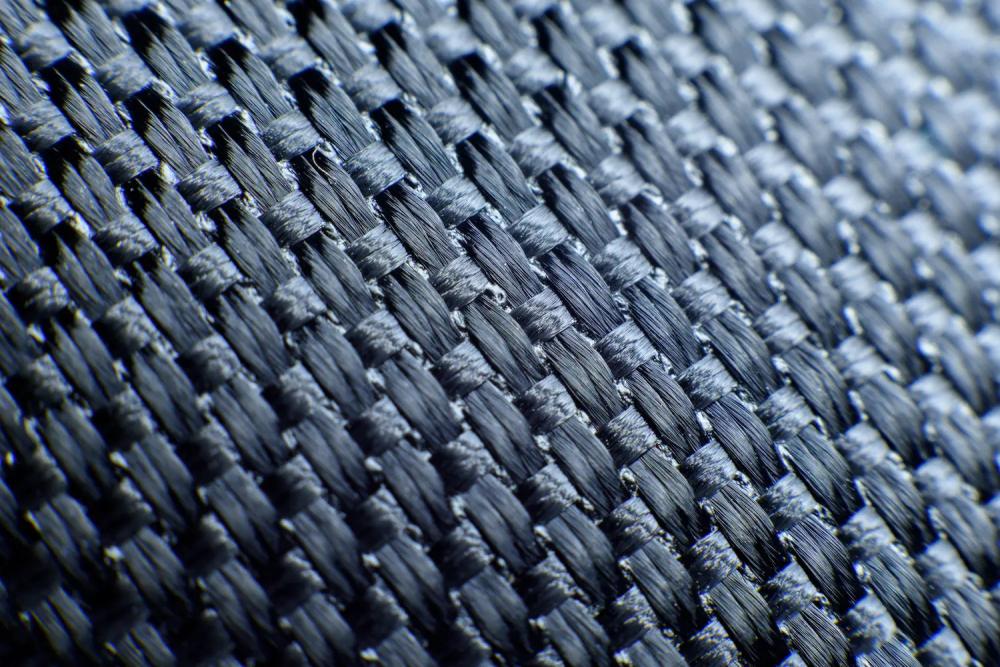
Carbon Fiber Prepregs
Carbon fiber prepregs provide industry-leading strength-to-weight performance, making them ideal for aerospace, automotive, and high-performance sports applications. Makobond carbon fiber prepregs are available in a variety of resin systems including epoxy, BMI, polyimide, and cyanate ester,ensuring optimal performance for specific project requirements. These composite materials deliver superior stiffness, fatigue resistance, and impact durability, enabling manufacturers to produce lightweight yet highly durable parts for demanding structural applications.
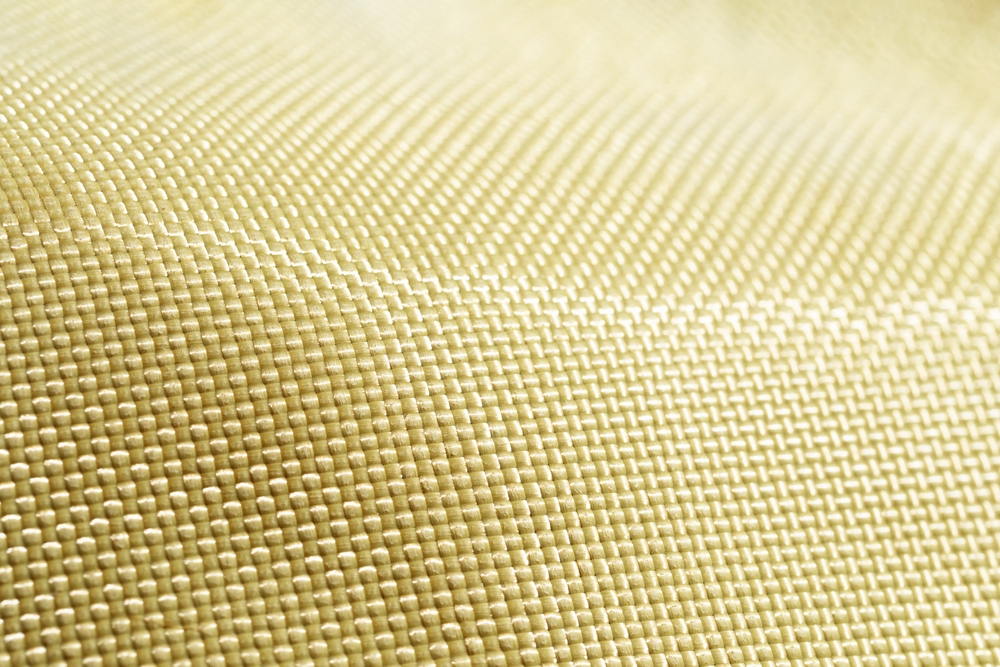
Kevlar Aramid Prepregs
Kevlar® aramid prepregs are engineered for exceptional toughness, impact resistance, and energy absorption. Ideal for defense, transportation, and sporting goods industries, Makobond Kevlar® Aramid prepregs offer lightweight protection against ballistic forces and punctures. These aramid fiber prepregs are commonly used in aerospace panels, armor systems, and high-impact structural parts. Kevlar prepregs combine high strength and low weight, making them a preferred choice for advanced composite applications requiring durability and safety.
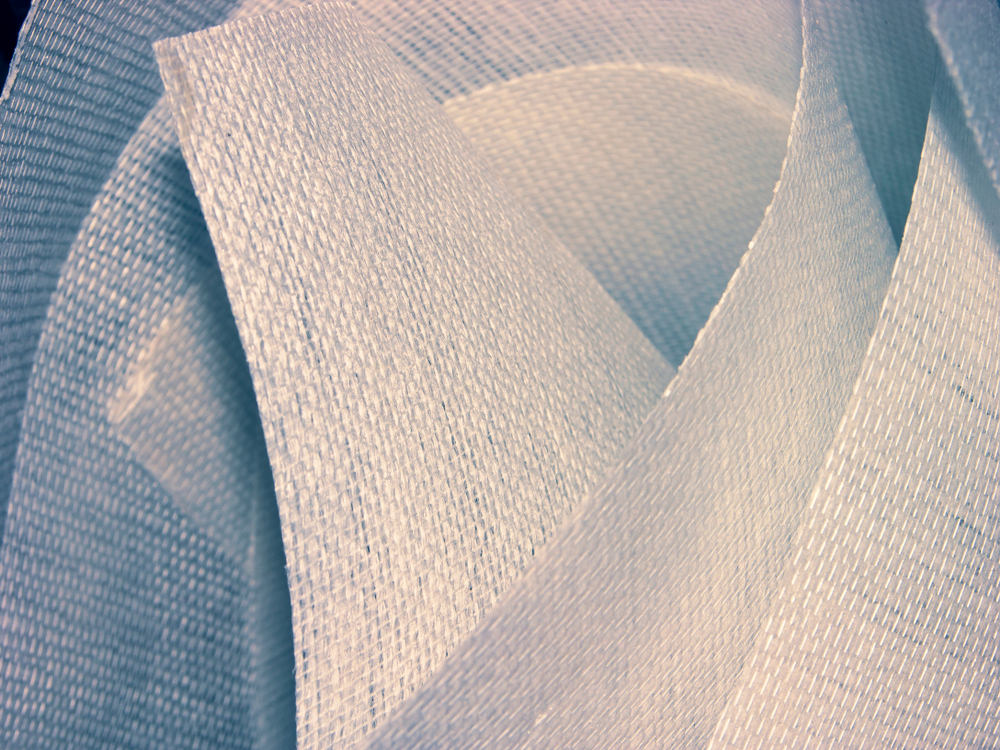
Fiberglass Prepregs
Fibreglass prepregs provide an economical solution for manufacturers seeking a balance of performance and affordability. Makobond fiberglass prepregs are ideal for aircraft interiors, marine structures, and industrial applications. With excellent corrosion resistance, fatigue performance, and ease of processing, fiberglass prepregs are a go-to material for both structural and cosmetic parts. These glass fiber-reinforced prepregs help reduce weight while maintaining strength and reliability, making them a popular choice for cost-effective composite manufacturing.
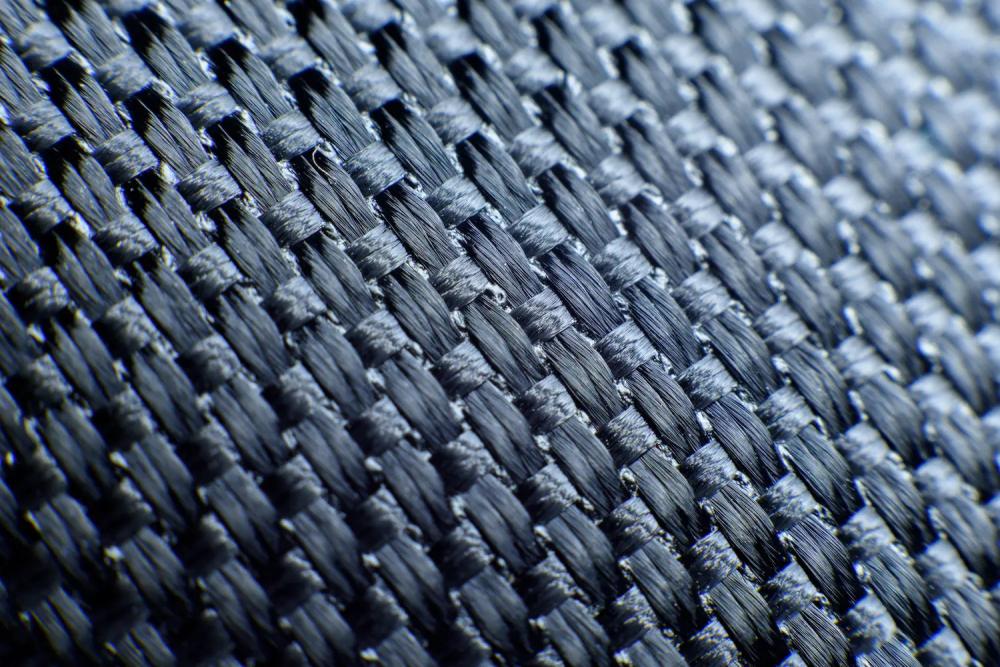
Tooling Prepregs
MakoTool prepregs are specially formulated to produce high-strength, dimensionally stable molds and tools for composite part manufacturing. Makobond tooling prepregs offer low shrinkage, excellent surface finish, and thermal stability, enabling manufacturers to create reliable tools for repeated use. Ideal for aerospace, automotive, and industrial production, these prepregs ensure high-quality mold surfaces and structural integrity, reducing production downtime and improving part consistency. MakoTool formulas offer low initial cure temp and high Tg service temp, and can save time in expensive autoclave cure with variable cure and post-cure options.
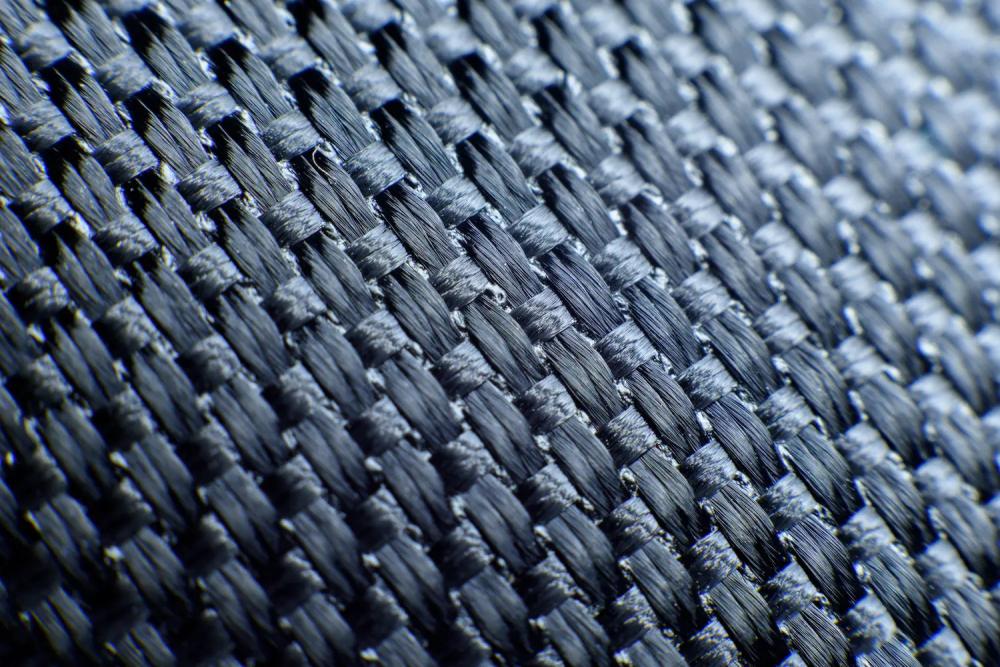
Cyanate Ester Prepregs
Cyanate ester prepregs are high-performance composite materials designed for applications requiring low moisture absorption, excellent thermal stability, and superior dielectric properties. Makobond cyanate ester prepregs are commonly used in radomes, antenna structures, and aerospace components operating in extreme environments. These prepregs maintain mechanical and electrical performance in high humidity and elevated temperatures, making them ideal for defense and telecommunications applications.
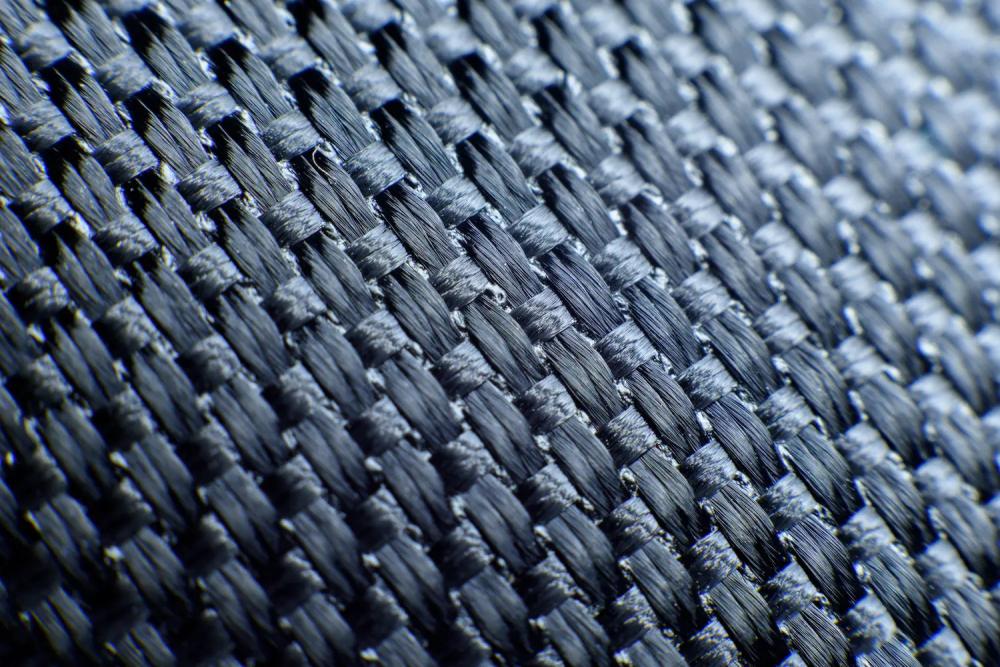
Polyimide Prepregs
Polyimide prepregs are ultra-high temperature composite materials capable of withstanding temperatures above 500°F (260°C). The Makobond Polyimide is formulated with a new addition-cure chemistry that replaces any polyimide currently used. Improvements include lower volatiles, easier processing, fewer delaminations, and safer handling. Makobond addition-cure polyimide prepregs are ideal for aerospace engine parts, heat shields, and industrial applications requiring long-term thermal stability, and they offer the added benefit of lower volatiles while curing. These prepregs offer superior chemical resistance and mechanical performance under extreme conditions, making them the material of choice for mission-critical aerospace and industrial environments.
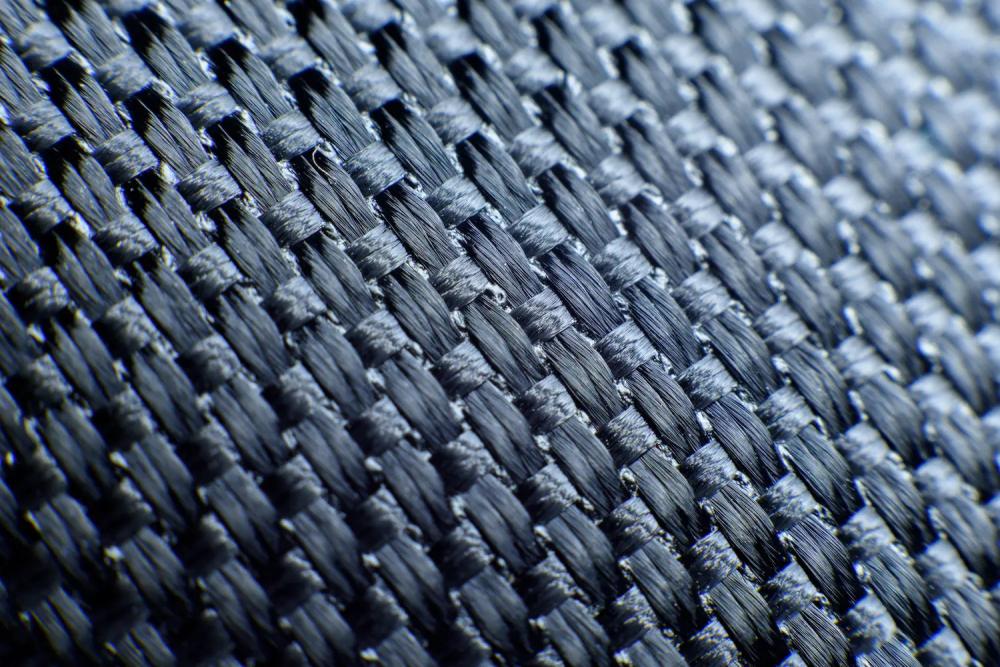
Radome Prepregs
Radome prepregs are engineered for optimal RF (radio frequency) transparency while maintaining structural and environmental durability. Makobond radome prepregs are trusted in aerospace and defense industries for protecting sensitive radar and communication systems without interfering with signal transmission. Designed to withstand harsh weather and thermal cycling, Makobond low-dielectric prepregs provide long-lasting performance in aircraft radomes, ground-based antenna covers, and telecommunications structures.
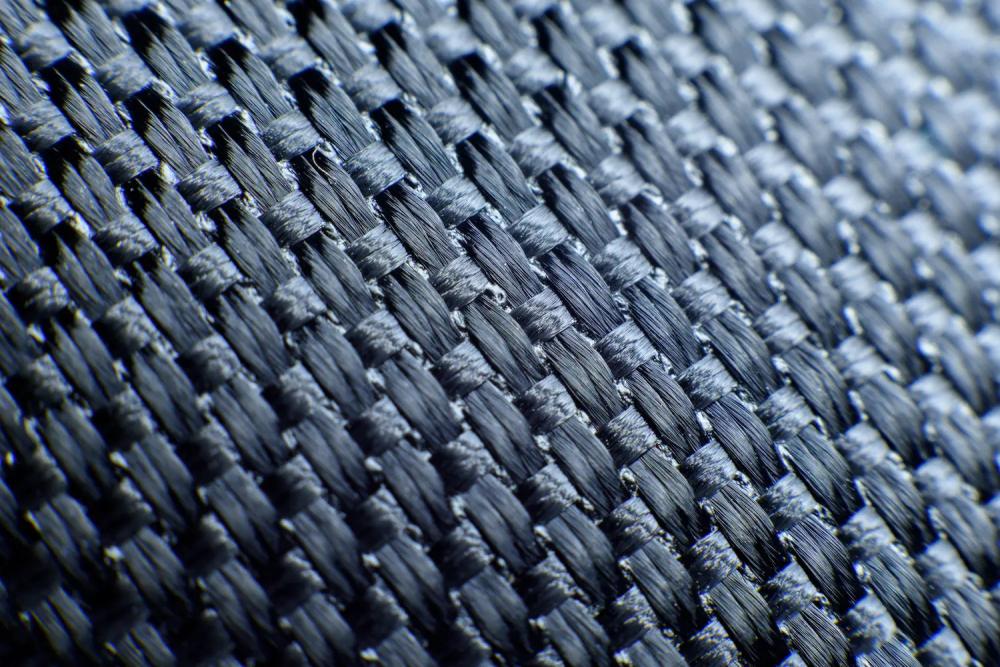
Flame Retardant Prepregs
Flame retardant prepregs are critical for meeting fire, smoke, and toxicity (FST) regulations in aerospace, mass transit, and building materials. Makobond flame retardant prepregs deliver outstanding fire safety without sacrificing mechanical performance. These self-extinguishing composite materials are ideal for aircraft interiors meeting FAR25.853, train components, and architectural applications where passenger safety and compliance with strict fire safety standards are required. Makobond FR prepregs are formulated to pass vertical burn, smoke density, and heat release in compliance with FAR25.853 and other industry standard specifications.
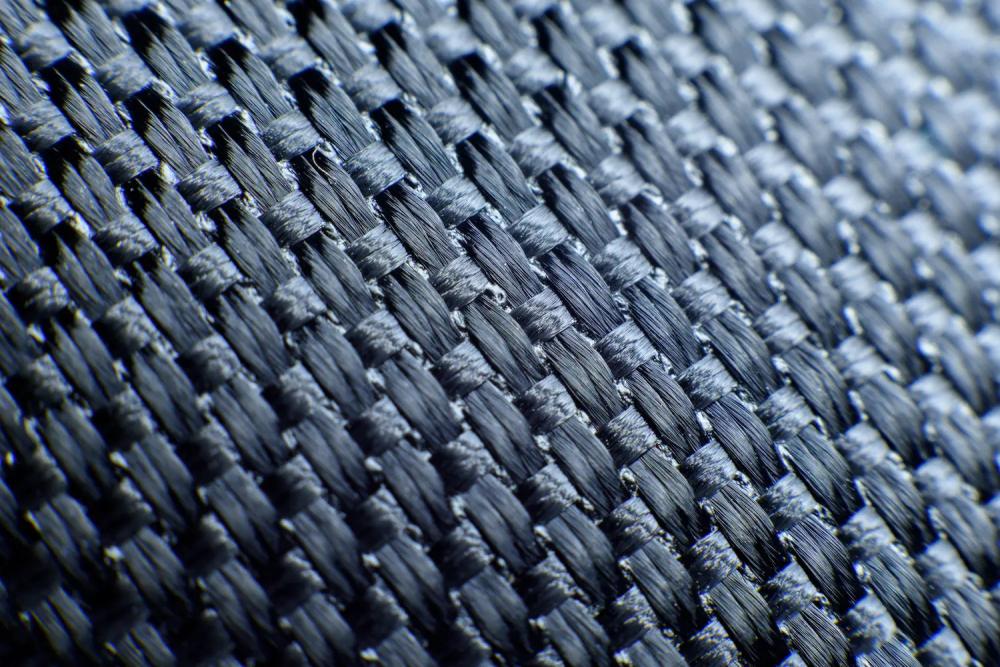
Qualified Aerospace Prepregs
Makobond’s qualified aerospace prepregs are engineered and tested to meet the strictest aerospace industry standards for strength, durability, and process consistency. Used in critical aerospace structures, interior components, and defense systems, these prepregs offer certified performance backed by complete traceability and quality assurance. Manufacturers worldwide rely on Makobond’s aerospace prepregs for FAA-compliant, military-grade, and commercial aircraft applications, ensuring safety and reliability at every altitude.
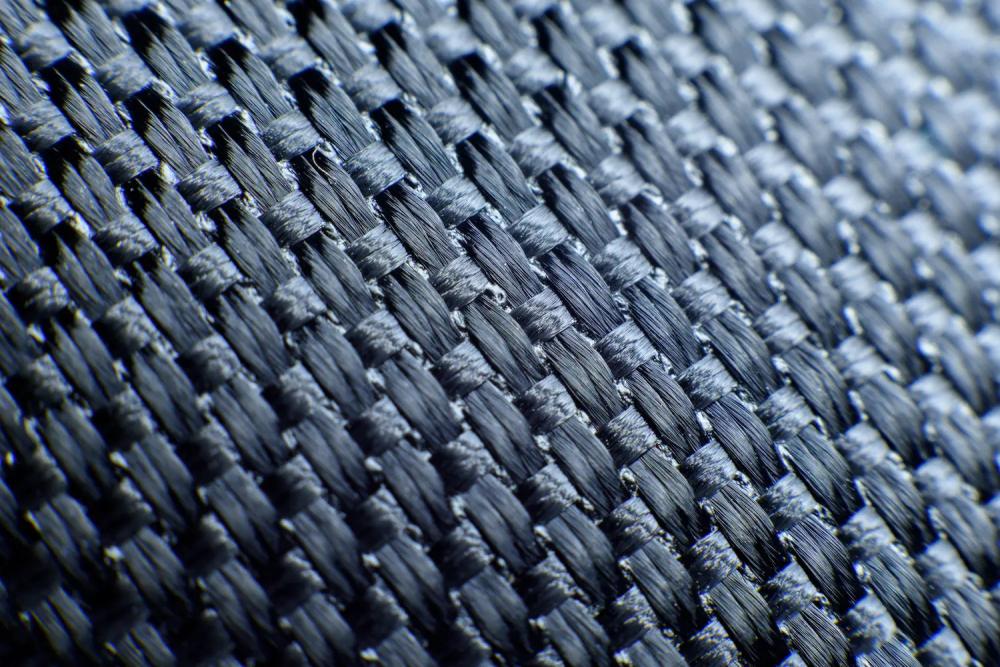
HyperCure Prepregs
Makobond's "P-2244 HyperCure" is a rapid cure, higher temperature and performance structural epoxy resin system engineered for high volume composite manufacturing. Ideal for small to large structures requiring enhanced toughness and shorter cure cycles, P-2244 excels with demanding aerospace parts. Its broad curing range make it the most robust material to qualify into new unmanned platforms that might see increased volume.
ID | Name | Description | Tg | Common Types | Cure Options | Lead Time |
---|---|---|---|---|---|---|
P-2000 | Makobond P-2000 Cosmetic FR Prepreg |
We combined the most requested features into one prepreg to meet 95% of fabrication jobs! P-2000 epoxy prepregs are flame-retardant, variable temp cure, high-strength, cosmetic high-clarity, good outlife and shelf life, short lead time and great value. Coated on carbon, aramid, or fiberglass fabrics, these prepregs are perfect for industrial, marine, automotive, aerospace, and sporting goods. | 281F (138C) or 305F (152C) for HT version | P-2000-C 282 (3k PW, 200 gsm) 284 (3k twill, 200 gsm) 670 (12k twill, 670 gsm) P-2000-A 120 (58 gsm) 285 (4HS, 170 gsm) P-2000-F 120 (4HS, 106 gsm) 7781 (8HS, 295 gsm) | Variable Temp Cure Refer to TDS | 2-4 Weeks ARO |
P-2100 | Makobond P-2100 Adhesive Prepreg | Makobond P-2100 self-adhesive prepregs deliver exceptional peel strength, toughness, and flame retardance for demanding applications. Designed to bond directly to core materials, it can eliminate the need for extra adhesives, streamlining production. With flexible curing options and FAR Part 25.853 compliance, it's perfect for aerospace, automotive, and other industries where safety and durability are key. | Service Temp 225F (107C) | P-2100-C 282 (3k PW, 200 gsm) 284 (3k twill, 200 gsm) 670 (12k twill, 670 gsm) P-2100-A 120 (58 gsm) 285 (4HS, 170 gsm) P-2100-F 120 (4HS, 106 gsm) 7781 (8HS, 295 gsm) | 275F (135C), 40min 250F (121C), 60min 235F (113C), 90min | 2-4 Weeks ARO |
P-2206 | Makobond P-2206 Extra-tough Prepreg | Makobond P-2206 is a highly toughened epoxy prepreg designed for advanced composites requiring superior surface quality, high mechanical performance, and thermal reliability. It supports variable temperature curing via vacuum bag oven, trapped rubber molding, or autoclave, delivering void-free, smooth finishes for laminates and sandwich structures. With a service range of -67°F to 250°F, it offers excellent thermal, UV, and fluid resistance. P-2206 suits automotive, aerospace, and sporting goods applications, providing strength and visual appeal for demanding uses. | 265F (129C) | P-2206-C 282 (3k PW, 200 gsm) 284 (3k twill, 200 gsm) 670 (12k twill, 670 gsm) P-2206-A 120 (58 gsm) 285 (4HS, 170 gsm) P-2206-F 120 (4HS, 106 gsm) 7781 (8HS, 295 gsm) | 250F (121C), 35min 235F (113C), 60min 200F (93C), 4hr 180F (93C), 8hr | 2-4 Weeks ARO |
P-2244 | Makobond P-2244 HyperCure Prepreg | P-2244 HyperCure is a rapid cure, higher temperature and performance structural epoxy resin system engineered for high volume composite manufacturing. Ideal for small to large structures requiring enhanced toughness and shorter cure cycles, P-2244 excels with demanding aerospace parts. Its broad curing range make it the most robust material to qualify into new unmanned platforms that might see increased volume. | Up to 353F (178C) | PP-2244-C 282 (3k PW, 200 gsm) 284 (3k twill, 200 gsm) 670 (12k twill, 670 gsm) P-2244-A 120 (58 gsm) 285 (4HS, 170 gsm) P-2244-F 120 (4HS, 106 gsm) 7781 (8HS, 295 gsm) | 180F to 350F Refer to TDS | 2-4 Weeks ARO |
P-2318 | Makobond P-2318 Tooling Prepreg | P-2318 is a high-performance tooling prepreg system with a thermosetting epoxy matrix, designed for low-temp initial cure/high temp service. It cures at 55-80°C (131-176°F) with variable post-cure options supporting continuous use up to 180°C (356°F). P-2318 ensures thermal stability, vacuum integrity, and exceptional durability for demanding composite tooling applications. | 410F (210C) | P-2318-C 284 (3k twill, 200 gsm) 670 (12k twill, 670 gsm) | 131F (55C), 24hr 140F (60C), 18hr 149F (65C), 12hr 158F (70C), 9hr 167F (75C), 7hr 176F (SOC), 5hr | 2-4 Weeks ARO |
P-2603 | Makobond P-2603 Polymide Prepreg | High-performance, modified addition-cure polyimide prepreg with a Tg above 600°F (316°C), offering exceptional thermal and mechanical stability. Fire-retardant and compliant with stringent aerospace, industrial, and automotive standards, it excels in tensile strength, flexural integrity, and dimensional stability under extreme conditions. With a wide service temperature range of -67°F to 640°F (-55°C to 338°C) and resistance to industrial fluids, P-2603 is versatile for autoclave or vacuum bag curing. Ideal for high-temperature insulation, aerospace ducting, electrical components, and structural laminates, it's the ultimate solution for demanding, fire-resistant applications. | 610F (321C) | P-2603-F 7781 (SHS, 295 gsm) | 350F or 375F Initial 450F or 475F Post Refer to TDS | 3-4 Weeks ARO |
P-2650 | Makobond P-2650 BMI Prepreg | Makobond P-2650 is a toughened BMI carbon prepreg designed for aerospace, defense, and high-performance industrial applications. With superior mechanical strength, thermal stability, and resistance to extreme environments, it excels in critical load-bearing structures. Offering continuous service at 400°F (204°C) and short-term capability up to 450°F (232°C), P-2650 delivers exceptional toughness, impact resistance, and reliability, even in hot/wet conditions. | 485F (252C) | P-2650-C 584 (3k SHS, 373 gsm) IM7 (6k 5HS, 376 gsm) P-2650-F 120 (4HS, 106 gsm) 7781 (SHS, 295 gsm) | 350F or 420F Initial 440F or 480F Post Refer to TDS | 3-4 Weeks ARO |
*The data provided is for informational purposes only and does not constitute a warranty. Users must verify suitability through testing. Refer to the SOS and label for safe handling instructions. This product is for industrial/commercial use, handled by trained personnel.